Air Cylinder Sizes Explained: How to Pick the Right Fit for Your System
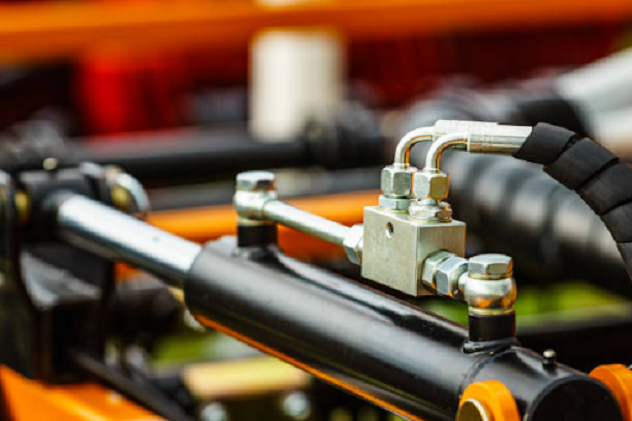
Size of an air cylinder is among the most important aspects to keep in mind when choosing pneumatic components for an industrial automation system. Choosing the right air cylinder sizes guarantees that the system functions at its optimum level, utilizing the required amount of power and stroke length needed for the application. It does not matter if you are building a new system or if you are improving an old one; what matters is that you understand the role cylinder size serves and how it affects performance. With the help of industrial automation suppliers, this guide will help you step by step to choose the correct air cylinder size with great tips on how to make the most of your pneumatic systems. If all the factors mentioned above are kept in consideration, selecting the proper air cylinder size will assist in eliminating system deficiencies, minimizing energy use, and enhancing system efficiency in all aspects which results in a significant amount of time and resources saved.
Gaining Insights into Air Cylinder Sizes
The bore diameter and stroke length are the two main parameters that determine air cylinder sizes. The bore diameter dictates the amount of force the cylinder can produce, while the stroke length indicates the distance that the piston is capable of moving. These two metrics are very important for the functioning of your system since they determine the speed, force and accuracy of your pneumatic operations. Industrial automation suppliers offer various sizes of air cylinders to fit different applications, from light-duty to heavy-duty industrial processes. Knowing how these measurements impact the system’s operation will aid in choosing the right cylinder to achieve the desired performance. Outfitting your system with the appropriately sized air cylinder can improve the productivity of your system by allowing the actuator to move at the optimal speed and force, thus preventing damage and increased wear on the actuator.
How Do Bore Diameters Affect the Performance of the Cylinders?
The bore diameter is defined as the internal distance of the cylinder in which the piston moves in and out. It is one of the most vital parameters regarding the magnitude of air pressure that an air cylinder can exert. As the bore diameter increases, so too does the force that the cylinder can produce. In the case of pneumatic systems, the force is the result of the application of pressure on the surface area of the piston. Increased surface area of the piston enables the norm to be generated by the cylinder and is ideal for extremely high duty cycles. However, reduced diameters are optimal for systems that require precise control as well as less force such as in light duty applications. Practically, when selecting the sizes of the air cylinder, one must work with the industrial automation suppliers so that both the right sized bore diameter which balances force consumption and energy efficiency is utilized. Choosing the correct bore diameter ensures that the seal will meet the required ‘force’ as well as load conditions of the particular application without undue straining on the system leading to enhanced output and improved service life.
Stroke Length: What You Need to Know
When it comes to the stroke length of an air cylinder, it speaks of how much a piston can move within the cylinder. This measurement is crucial for analyzing the potential motion range for your system. Clearly defined stroke length ensures that a pneumatic system performs the prescribed task without being overextended or underused. For example, when you need to reposition a part of the workpiece from one place to another on a conveyor belt, the stroke length must be sufficient enough to cover the distance, but not too much as it would consume too much air and put too much mechanical strain. Stroke length of air cylinders differs, as do their sizes, and industrial automation vendors can help you choose the one that fits for the specific distance that the actuator should cover in your system. It is important to precisely define the stroke length of the actuators in your pneumatic automation system to guarantee unobstructed and efficient functioning. It helps avoid the usage of excess air for the automation system to work within the needed boundaries, which reduces operational cost and improves efficiency.
Pressure and Performance of Air Cylinder
Bore diameter and stroke length are the two main aspects used when trying to accurately determine the ideal size of the air cylinder. An operating system’s pressure has a significant influence as well. Pneumatic systems utilize compressed air for motion, and the supplied pressure is directly proportional to the force and velocity that the piston can generate. Generally, faster movement and higher force would be observed with increased pressure, but stress on the cylinder and other components of the system grows, risking damage. It is important to note that the pressure rating of your air cylinders should conform with the operating parameters of your pneumatic systems to maximize efficiency and the expected lifespan. When setting the pressure rating, industrial automation suppliers can provide useful information regarding how performance can be maximized while still being within the safety limits. Correct pressure settings are geared towards the reliable performance of the system while minimizing stress on the components, hence increasing the system’s life span as well as its efficiency.
Conclusion
In every Automation system, choosing the right air cylinder size involves careful consideration of bore diameter, stroke length, and operating pressure, especially if one seeks high performance. To optimize the functionality of the pneumatic system, it is prudent to engage with industrial automation suppliers. Right sizing contributes to the assistive force, stroke range, energy consumption, and service life of the cylinder. Achieving correct sized cylinders guarantees smooth and reliable operation, which complements the overall performance of the industrial automation system. It is a simpler task when dealing with reputable suppliers as any outdated system or system primed from scratch will meet the user’s needs. Increased system performance, decreased downtimes, and several year savings are the ultimate outcomes of prudent cylinder selection for any industrial automation system.